How to choose a welding machine?
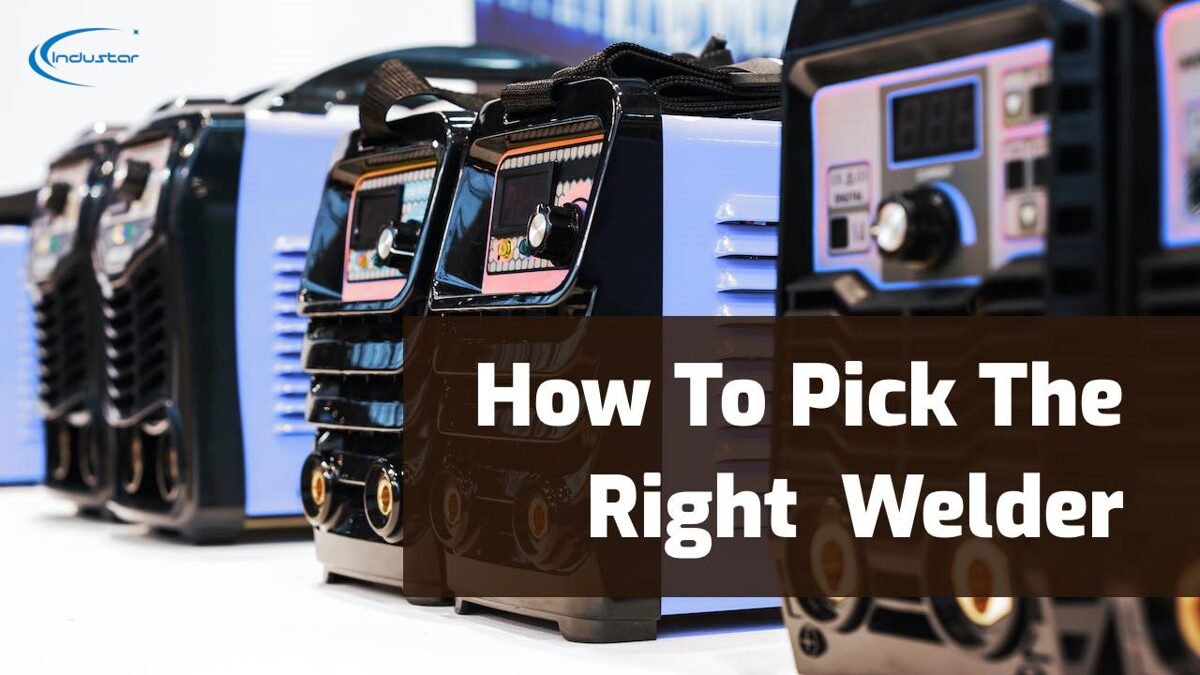
Welding equipment is very often needed for work in a private yard, country house or garage. Most modern devices are designed according to the inverter scheme. Thanks to this, the device has gained compactness and lightness. The inverter unit does not take up much space in the trunk of the car and is also easy to carry in the hands. Despite the small weight and dimensions, the inverter allows you to perform quite serious welding work at a professional level. The choice of a welding inverter is made taking into account the functions that it will have to perform and, of course, with an acceptable purchase budget.
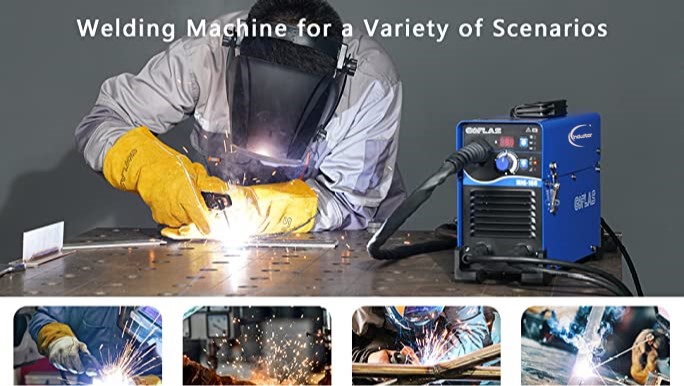
Choose MMA with an electrode welding machine!
Devices of this type represent the initial price segment of welding inverter equipment. Manual welding involves the use of replaceable conventional electrodes.
These devices are capable of performing almost all welding work that may be required in a household.
According to technical capabilities, welding inverters are divided into professional and amateur. Sometimes another gradation is used - semi-professional devices.
Before choosing an inverter-type welding machine, you should carefully understand what technical parameters determine whether the machine belongs to one or the other category.
Functions are important for welding machines!
Inverter welding current value;
Duration of inclusion, denoted by PV;
Nominal supply voltage and its permissible deviations;
The presence of additional functions.
The maximum value of the welding current is the very first characteristic that is paid attention to when choosing a welding machine. The current determines the permissible thickness of metal that the selected home welding equipment can work with. The current value is directly related to the diameter of the selected electrode.
Based on this, you should choose an inverter for your needs, taking into account the thickness of the metal you have to work with. The relationship between the thickness of the workpiece, the diameter of the electrode and the required welding current can be selected from the tables, which are often found in the instructions for use of the inverters and are printed on the electrode packages. For example, to weld a metal with a thickness of 3 mm, you should choose an electrode with a diameter of 3 mm and set a welding current of 65-100 amperes.
Welding machine start-up, duration of work!
In addition to the amperage, the so-called duty cycle (PV), usually expressed as a percentage, is indicated in the table of technical parameters of the device. In general, this value characterizes the permissible operating intensity of the apparatus, that is, it determines the limiting relationship between the duration of welding periods and work interruptions.
Make the right choice when looking for a welding machine!
The following is the technique for evaluating the characteristics of welding equipment... The basis is the operation cycle of the inverter, the duration of which is 10 minutes. The switching-on time specified in the parameters determines how much of this period the inverter can be in welding mode.
The duty cycle is closely related to the amperage. For example, the instruction may indicate: duty cycle is 50% at 200 amp current, 100% at 120 amp current. This means that at 200 amperes the inverter should be in welding mode for no more than five minutes in ten minutes, at 120 amperes the welding mode can be constant.
Working time is one of the main parameters by which inverters are classified as professional or amateur devices.
Any inverter model has overheating protection. Choosing a welding inverter with good current and duty cycle margin will allow it to operate at a lower stress and last longer. On the other hand, the price of such a device should be higher.
Looking for a welding machine is the connection important?
As for the supply voltage of the inverter welding machine, it is preferable to choose a single-phase device in which the power source is provided from a 220-volt network. Three-phase power supply in domestic conditions is not common, such a design of inverters is typical for more powerful industrial needs.
When choosing a welding inverter, you should pay attention to the permissible deviation range of the supply voltage specified in the manual. This is an important indicator that allows you to work in conditions of poor quality nutrition. It should be noted that the inverter transformation principle itself means much less dependence on the supply voltage level compared to conventional welding transformers.
Welding inverters from different manufacturers have very similar converter circuits, but there are differences in the technical data tables in terms of the permissible values of the network voltage. When choosing, of course, preference should be given to devices that have a wider range of values.
Additional options of the welding machine!
Modern welding inverters can have several additional functions that make the welding process more convenient and, as a result, allow you to get a better result. It is advisable to choose the device taking into account the following arguments:
Electric arc forcing function Arc Force;
Automation that ensures easy ignition of the hot start arc;
Preventing electrodes from sticking during Anti Stick arc ignition;
Availability of digital indication of welding current level.
All the above functions are implemented in inverters quite simply, without much circuit complexity. This is explained by the fact that the current regulation in these devices is carried out by electronics, and the creation of additional control circuits does not lead to a significant increase in the cost of the product.
When choosing, it should be taken into account that the cost of inverters that have all the above functions may not be practically different from the cost of devices that do not have them.
Inverter machine for semi-automatic MIG/MAG welding
If funds allow and there is a desire to choose the most modern tool with wider functions, you can stop at the semi-automatic device of the middle price category, which is also related to inverter-type devices.
Which welding machine is better?
Semi-automatic inverter-type welding machines open up possibilities for welding joints that are not available with manual welding machines. First of all, it is about welding thin sheet materials, as well as welding cast iron, stainless steel and non-ferrous metals.
Semi-automatic welding has its own characteristics. A thin welding wire is used as an electrode. Mounted on a rotating spool, it is continuously fed automatically into the welding zone. Welding is performed in a protective gas environment. These can be inert gases, argon or helium, or active carbon dioxide. Thus, the consumables here are welding wire and gas. Welding with a semi-automatic inverter is an even simpler procedure than working with a manual welding machine, here even a beginner who encounters this process for the first time can create a high-quality seam.
Now the choice is yours!
Welding inverter choices, here are three types of welding process. It is manual arc welding, as well as welding in an environment of inert and active gases. There is another technology - it is welding with an unusable electrode in an argon environment. This type of welding is very popular when working with aluminum and its alloys. And not only. In this way, a perfect seam is created, connecting products from black and stainless steel, non-ferrous metals.
All four of the mentioned welding technologies are implemented with devices based on one type of inverter welding current sources. This gave manufacturers the idea to combine all functions in one device.
By choosing a 4 in 1 inverter, you will be able to equip your garage with a real mini-equipment for the price of one semi-automatic inverter.
1 comment - How to choose a welding machine?
Leave a reply
Cart
Cart is empty.