Welding shielding gases - briefly
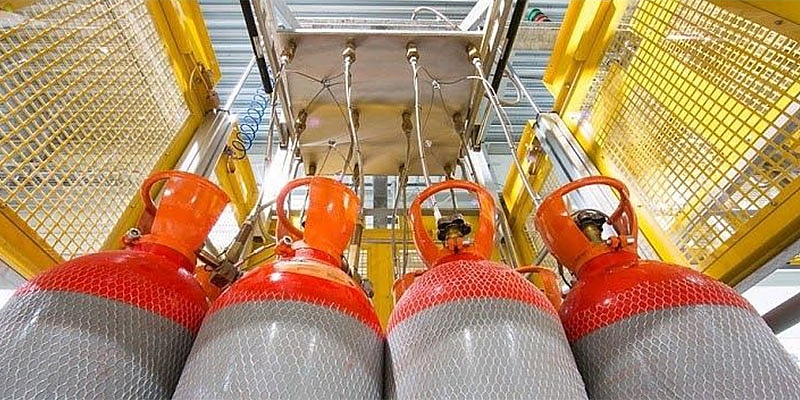
Technical Gases in Welding: CO₂, Argon, and Argon-CO₂ Mixtures
The choice of shielding gas in welding has a significant impact on the final result – weld quality, process efficiency, and overall cost. Different gases are used depending on the welding method, materials, and desired outcome. Let’s take a closer look at the most common gases – carbon dioxide (CO₂), argon, and argon-CO₂ mixtures, their characteristics, and their applications.
1. Carbon Dioxide (CO₂)
CO₂ is an economical and widely available gas commonly used in steel welding.
- Properties:
CO₂ is an active gas that reacts with the base material during welding. It provides deep penetration and creates a robust weld joint. - Applications:
- Used in MIG/MAG welding.
- Ideal for welding thick steel and construction materials.
- Frequently applied in industrial projects where durability is prioritized over appearance.
- Advantages:
- Affordable and effective for thicker materials.
- Suitable for heavy-duty and large-scale projects.
- Disadvantages:
- Produces more spatter compared to other gases.
- Weld surfaces may lack a smooth, aesthetic finish.
2. Argon (Ar)
Argon is an inert gas that ensures high-quality and precise welds.
- Properties:
Being chemically inactive, argon creates a protective layer around the welding area, preventing oxidation and ensuring a stable arc. - Applications:
- Used in TIG MIG welding, especially for non-ferrous metals (aluminum, copper) and stainless steel.
- Suitable for thin materials and projects requiring aesthetic welds.
- Advantages:
- Clean and smooth welds.
- Minimal spatter formation.
- Ideal for precise and delicate tasks.
- Disadvantages:
- Higher cost compared to CO₂.
- Less effective for welding thicker materials.
3. Argon-CO₂ Mixtures
These mixtures offer a versatile solution, combining the benefits of argon and CO₂.
- Properties:
Typical mixtures contain 75–95% argon and 5–25% CO₂. This semi-active gas mixture provides a stable arc, good penetration, and reduced spatter. - Applications:
- Commonly used in MIG/MAG welding for both thin and medium-thickness steel.
- Ideal for versatile applications where both quality and practicality are important.
- Advantages:
- Produces less spatter compared to pure CO₂.
- More stable welding process.
- Cleaner welds, suitable for a wide range of projects.
- Disadvantages:
- More expensive than CO₂.
What Do Professionals Choose?
- CO₂: Professionals use this for cost-effective solutions in heavy-duty construction and thicker steel materials.
- Argon: A top choice for TIG welders working with aluminum, stainless steel, or other non-ferrous metals. It’s essential for achieving high-quality, aesthetic welds.
- Argon-CO₂ Mixtures: A versatile option favored by both beginners and professionals for MIG/MAG welding and projects involving various steel thicknesses.
Conclusion
The choice of gas depends on your needs and project requirements:
- Opt for CO₂ for cost savings and deep penetration in heavy materials.
- Choose Argon for precision and superior weld quality.
- Go with Argon-CO₂ mixtures for a balanced and practical solution.
Selecting the right gas not only ensures a technically sound weld but also enhances its visual appeal.
How to find us!?No comments
Leave a reply
Cart
Cart is empty.